Tesla erbjuder redan rabatter på Cybertrucken
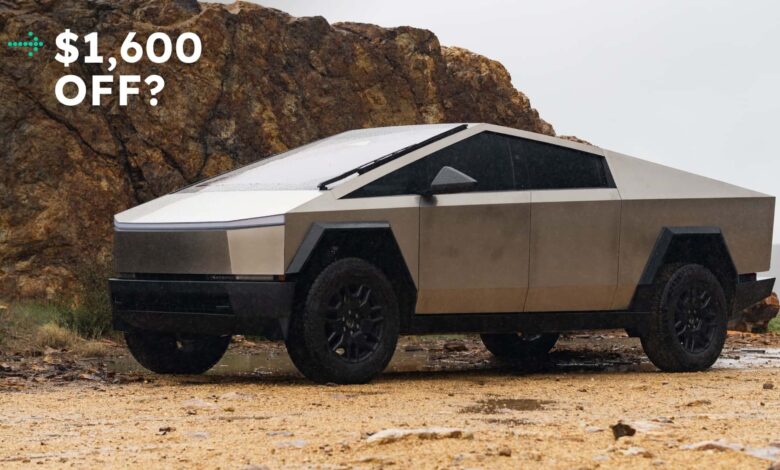
- Tesla erbjuder rabatter på upp till $2 630 på Cybertrucks.
- De rabatterade Cybertruckarna verkar dock inte vara berättigade till det federala köpincitamentet på $7 500.
- Om du personligen kvalificerar dig för det federala skatteavdraget rekommenderar vi ändå att du beställer en ny Cybertruck.
Den icke-Foundation Series-versionen av Tesla Cybertruck kom ut på marknaden först i slutet av förra året, men den har redan märkts ner. Lagerenheter kan hittas för $1 600 rabatt. Om du hittar en lastbil som användes som demofordon kan du få den ännu billigare.
Det betyder att du kan få en Cybertruck fyrhjulsdrift i lager för cirka 78 390 $, eller 77 360 $ om lastbilen användes som en demonstrationsenhet. Det är en märkbar rabatt från baspriset på 79 990 $, men observera att alla dessa priser exkluderar avgifter.
Det är också viktigt att notera att även om Cybertrucken nu är berättigad till ett federalt incitament för inköp av rena fordon på $7 500 – förutsatt att du inte är över inkomstgränsen – tror jag att de flesta om inte alla dessa lastbilar byggdes innan de blev berättigade. Du kan fortfarande dra nytta av $7 500 incitamentet om du köper lastbilen som ett kommersiellt fordon eller leasar den, men det finns ingen indikation på Teslas webbplats att du kan göra anspråk på den själv.
Rabatten är bra för konsumenterna, men det är oklart vad det betyder för Tesla. Företaget sänkte redan effektivt priset på Cybertrucken med 20 000 dollar när det introducerade modellen som inte kom från Foundation-serien i slutet av förra året. Det stimulerade även lastbilarna i slutet av året. Tesla erbjöd gratis Supercharging för livet för nya Cybertruck-köpare i slutet av december. Trots det sjönk försäljningen fortfarande med över 10 % på kvartalsbasis. Med tanke på att Q4 vanligtvis är den största månaden för konsumtionsutgifter, är det ett oroande tecken på att hypen kan ta slut.
Ändå är det heller ingen överraskning att Tesla försöker rensa ut lagret nu när nya lastbilar kvalificerar sig för skatteavdraget. Uncle Sam ger dig i praktiken 10 % rabatt på en ny Cybertruck, även om det måste vara basmodellen med tanke på kreditens 80 000 USD MSRP-tak. Så om Tesla har icke-kvalificerade baslastbilar som sitter runt, är det ett bra tillfälle att få bort dem från böckerna.
Om du vill ha en Cybertruck är det troligtvis bättre att leasa en lastbil eller köpa en ny som kvalificerar för skatteavdraget. Men om du inte personligen kvalificerar dig eller om du planerar att registrera lastbilen som ett nyttofordon, är detta ett sätt att spara ytterligare två tusenlappar. Det är aldrig en dålig idé.
Kontakta författaren: Mack.Hogan@insideevs.com.