2025 Jeep Wagoneer S är billigare, men det finns ett köp i appen
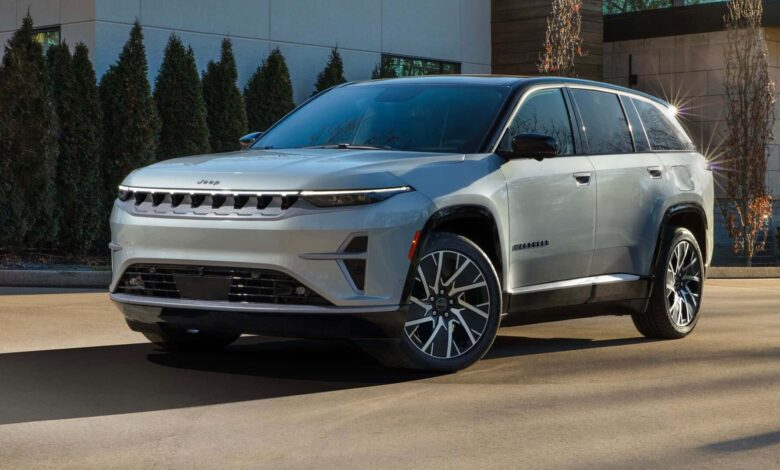
- Base Jeep Wagoneer S Limited går med i lanseringsutgåvan.
- Det är $ 5 000 billigare, men om du vill ha mer kraft måste du betala.
Jeep Wagoneer S fick precis en billigare begränsad trimnivå för 2025 -modellen. Det börjar på $ 66 995 inklusive destination, vilket är $ 5 000 mindre än lanseringsutgåvan som har alla klockor och visselpipor. Det är också berättigat till den federala skattekrediten på 7 500 dollar både vid köp och leasing.
För mindre pengar får du lite färre saker, som man kan förvänta sig. Jämfört med lanseringsutgåvan kommer 2025 Jeep Wagoneers Limited som standard med ett nedsatt ljudsystem och mindre kraft från det dubbla motoriska fyrhjulsdrivna systemet-500 hästkrafter istället för 600 hk.
Som sagt kan kunder välja att spendera lite mer för att få 920-Watts McIntosh-ljudsystem som erbjuds som standard i lanseringsutgåvan. Dessutom säger Jeep att det kommer att erbjuda ett betalt utdrivningspaket över luften som ökar den totala produktionen till 600 hk, samma som den dyrare lanseringsutgåvan. Det är mer eller mindre detsamma som ett köp i appen på din smartphone.

6
Den amerikanska biltillverkaren sa inte hur mycket dessa uppgraderingar skulle kosta, men det skulle inte vara vettigt ekonomiskt att rabattera dem, så om du är ute efter en 600 hk elektrisk medelstor SUV och går till toppresan från Get- GO kan vara det bättre valet, om än en dyrare på 5 000 dollar.
Den begränsade trimmen levereras med 20-tums hjul, ett maximalt användbart skärmutrymme på mer än 45 tum spridda över fyra skärmar, en myriad av säkerhetsfunktioner, 10-vägs uppvärmda framsäten och ett panoramatak med dubbla rutor. Det är detsamma som lanseringsutgåvan – motorerna och batteriet är troligen också detsamma.
Jeep nämnde inte ett körområde för de mer prisvärda Wagoneer S, men vi förväntar oss att det skulle vara detsamma som den dyrare trim-över 300 mil på en full laddning, enligt det Stellantis-ägda varumärket. På tal om laddning kan batteriet på 100,5 kilowatt-timme (användbart) fyllas på högst 203 kW från en kompatibel DC-snabbladdare, med 20-80% tid på 23 minuter. Företaget kommer också att kasta in en gratis 48-amp-nivå 2 hemladdare eller offentliga laddningskrediter för varje Wagoneers köp.